Dalam kondisi proses ekonomi modern yang berkembang secara dinamis, penciptaan prosedur produksi dan kontrol yang semakin kompleks, salah satu pendekatan yang paling relevan untuk peningkatannya adalah pengenalan metode untuk mengoptimalkan berbagai kerugian. Pertama-tama, ini menyangkut sumber daya perusahaan - sementara, keuangan, teknologi, energi, dan lainnya.
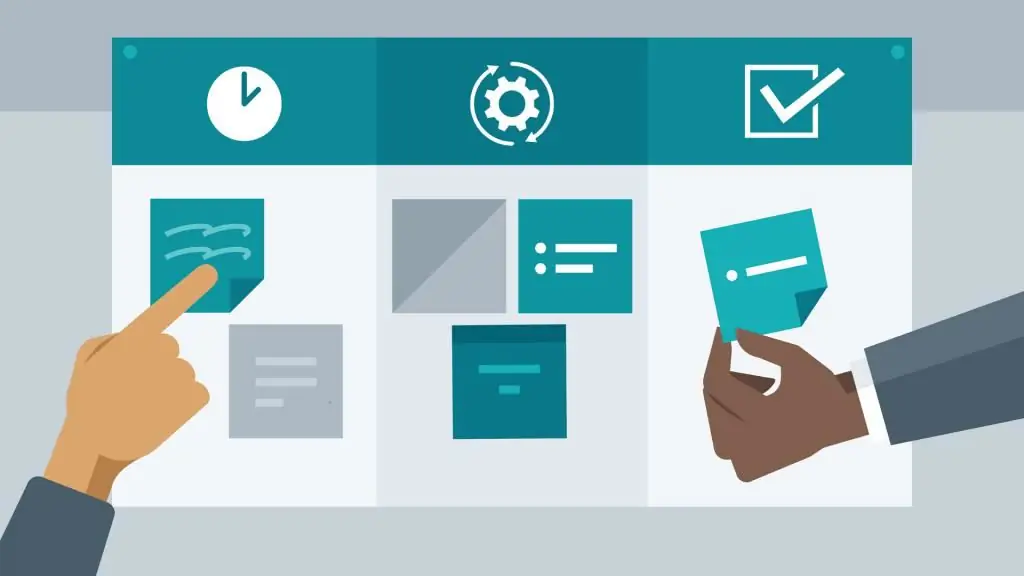
Fitur kegiatan
Dalam praktiknya, ada batas tertentu, yang dikaitkan dengan tingkat pengembangan teknologi dan organisasi sistem (organisasi, perusahaan). Jelas bahwa tidak pantas untuk menuntut otomatisasi total produksi dari bengkel jahit kecil sesuai dengan berbagai kriteria, dan di atas segalanya, yang ekonomis. Namun, terlepas dari ukuran sistem, perlu untuk memastikan penggunaan maksimum dan optimal dari sumber daya yang tersedia dengan kerugian minimal, yang berlaku untuk setiap organisasi dan aktivitas.
Dalam hal ini, menjadi perlu untuk menggunakan teknik manajemen proses progresif yang didasarkan pada teori menciptakan produksi lean atau "lean". Ini termasuk sistem 5S dan TPM, pemetaan aliran nilai dan SMED, dll.
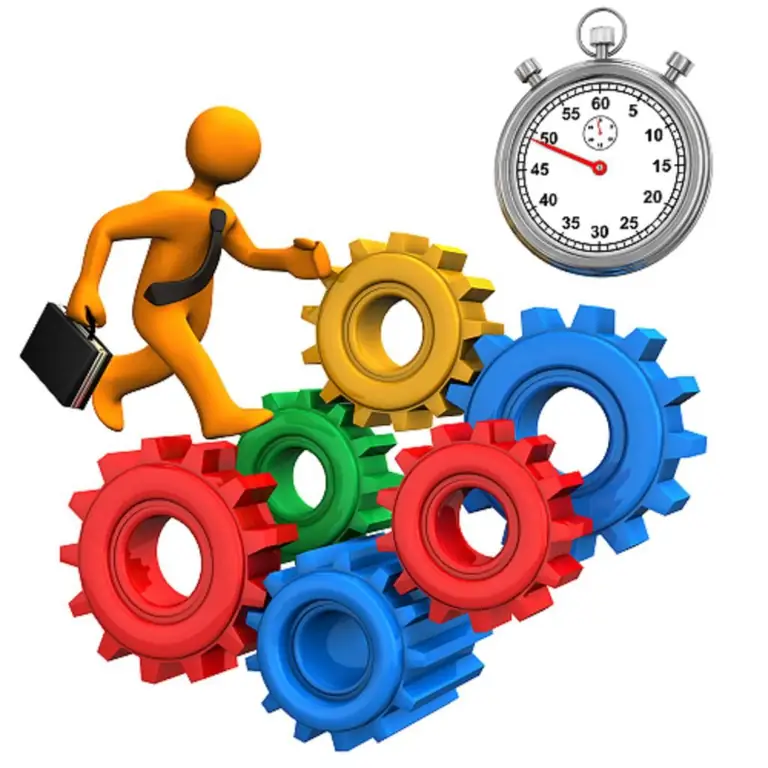
Tujuan inovasi
Produksi ramping ("lean") adalah sistem pendekatan khusus untuk organisasi kegiatan, yang menganggap tujuan utamanya menghilangkan berbagai kerugian dalam sistem. Mekanismenya cukup sederhana: segala sesuatu yang tidak menambah nilai bagi pelanggan harus diklasifikasikan sebagai berlebihan (pemborosan) dan dikeluarkan dari sistem. Jelas bahwa konsep "kerugian" adalah landasan, karena definisi mereka akan secara langsung mempengaruhi efektivitas metode. Dalam hal ini, belajar memetakan aliran nilai spesialis Anda adalah keuntungan yang signifikan di pasar pengiriman layanan
Jenis kerugian
"Lean manufacturing" adalah salah satu konsep dasar logistik produksi. Dan meskipun ada beberapa pendekatan berbeda untuk menentukan kerugian, kami akan memilih jenis yang paling universal:
- Waktu tunggu - setiap waktu henti dalam aktivitas mengurangi nilai produk akhir. Menunggu bahan, perbaikan peralatan, informasi atau arahan dari manajemen memperlambat proses dan meningkatkan biaya implementasinya.
- Operasi yang tidak perlu (pemrosesan produk yang tidak perlu) - operasi teknologi yang tidak perlu, tahapan proyek, semua yangdisediakan oleh prosedur standar, tetapi dapat diratakan tanpa kehilangan kepercayaan pelanggan.
- Pergerakan pekerja yang tidak perlu - mencari alat, peralatan, gerakan irasional karena organisasi tempat kerja yang buruk, dll.
- Pergerakan material yang tidak perlu - organisasi sistem inventaris yang buruk, kurangnya logistik transportasi yang progresif dan mekanisme outsourcing logistik.
- Kelebihan persediaan - mengikat modal kerja organisasi sebagai akibat dari pengeluaran yang tinggi untuk persediaan barang berlebih.
- Limbah teknologi - sistem pemrosesan data yang ketinggalan zaman, proses teknologi, dan rute pemrosesan.
- Kerugian produksi berlebih - produksi jumlah produk berlebih, yang menyebabkan peningkatan biaya penyimpanan, transportasi, dan penjualan selanjutnya.
- Kerugian intelektual - kurangnya mekanisme untuk mendorong inisiatif pekerja dan karyawan, sistem proposal rasionalisasi yang lemah, penekanan pendekatan kreatif untuk bekerja.
Salah satu metode paling umum untuk menghilangkan pemborosan sistem dan merampingkan pelaksanaan proyek adalah pemetaan aliran nilai. Manufaktur ramping pada saat yang sama memungkinkan Anda untuk membuat sistem adaptif yang secara fleksibel merespons perubahan lingkungan.
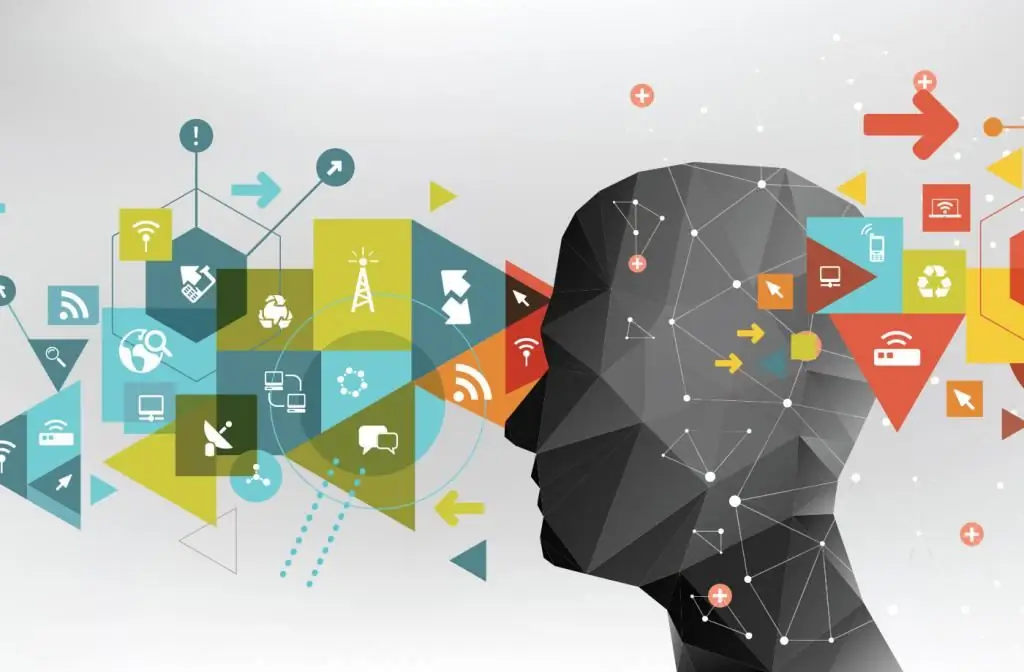
Aliran Nilai
Aliran nilai adalah kumpulan semua tindakan (operasi) yang dilakukan pada produk untuk mencapaikeadaan yang diperlukan atau memperoleh karakteristik yang diperlukan. Tindakan dibedakan menjadi dua kelompok:
- menciptakan nilai produk (adding value);
- tidak menambah nilai pada produk.
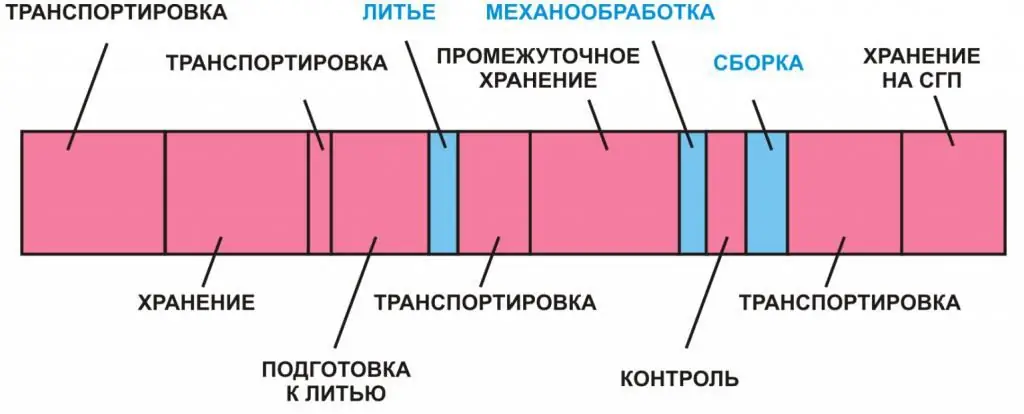
Seperti dapat dilihat dari gambar yang disajikan, tahapan perubahan teknologi produk (warna biru) menambah nilai produk, dan tahapan operasi tambahan - persiapan, transportasi, penyimpanan - (warna merah muda) - sebaliknya, lebih baik mengurangi nilai produk karena kehilangan waktu yang tidak perlu.
Proses pemetaan
Dasar dari teknik pemetaan adalah pengembangan algoritma grafis khusus yang menunjukkan proses pembuatan produk (implementasi proyek) tepat waktu. Algoritme ini disebut peta aliran nilai, yang merupakan model grafis berdasarkan kumpulan simbol (tanda, simbol) tertentu.
Kelebihan utama kartu:
- memperoleh model grafis dari proses yang sedang berlangsung, dengan mempertimbangkan berbagai proses tambahan untuk persepsi visual holistik (tugasnya adalah untuk melihat aliran umum peristiwa);
- kemampuan untuk mendeteksi berbagai jenis kerugian di semua tahap proyek;
- kemungkinan optimasi parametrik dari model yang dihasilkan untuk meminimalkan semua jenis biaya;
- bekerja dengan berbagai indikator algoritma, yang akan tercermin dalam peningkatan proses nyata.
Pembentukan value stream mapping berdasarkan grafik standar dansimbol - blok persegi panjang dan segitiga, panah terarah dan melangkah dan gambar lainnya. Ini memungkinkan untuk merekam tahapan proses yang sedang dipelajari dalam satu bahasa untuk semua spesialis. Pada saat yang sama, dianjurkan untuk membedakan simbol tergantung pada aliran yang dipertimbangkan - materi atau informasi.
Lean Value Stream Mapping memungkinkan Anda mengidentifikasi semua tempat di mana item yang tidak perlu menumpuk.
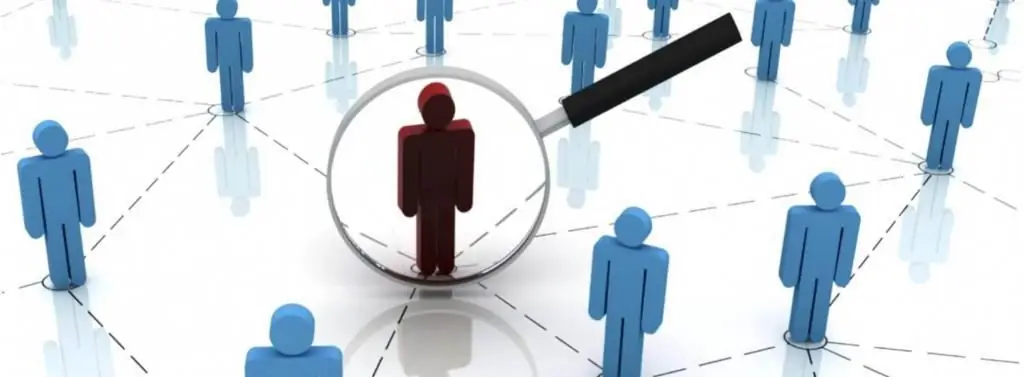
Aturan konstruksi
Pemetaan aliran nilai melibatkan serangkaian langkah sederhana yang akan dengan cepat membuat model proyek yang diperlukan dengan parameter yang diberikan. Misalnya:
- Lakukan analisis aliran material dan informasi untuk mendapatkan gambaran yang andal tentang keadaan proses saat ini.
- Melalui arus dalam arah maju dan mundur untuk mengidentifikasi penyebab kerugian yang tersembunyi dan menemukan pola negatif.
- Dalam keadaan apa pun, lakukan pengukuran waktu sendiri, tanpa bergantung pada hasil spesialis lain atau nilai standar.
- Jika memungkinkan, buat juga peta sendiri, yang akan memungkinkan untuk menghindari kesalahan orang lain dan solusi template.
- Fokus pada produk itu sendiri, bukan pada tindakan operator atau peralatan.
- Buat peta dengan tangan, menggunakan pensil atau spidol.
- Memvisualisasikan elemen proses menggunakan warna untuk meningkatkan persepsi.
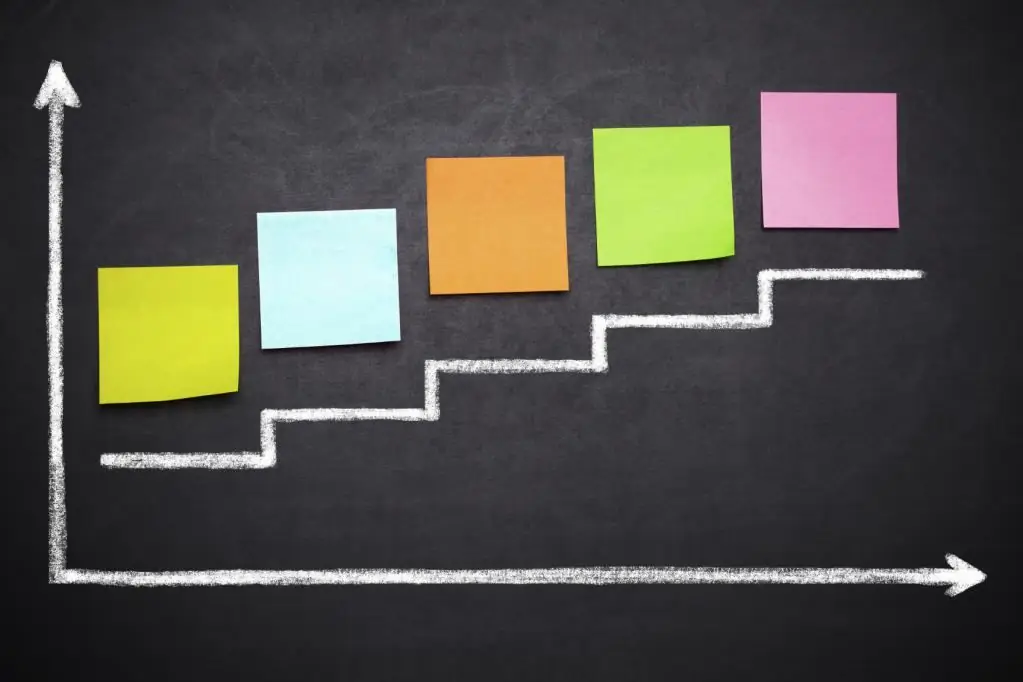
Contoh pemetaan aliran nilai
Mari kita perhatikan contoh pembuatan peta alur di bidang pengelolaan dokumen, yang melekat pada aktivitas lembaga mana pun.
Tugas utama adalah memilih pemasok terbaik. Proses keputusan standar adalah sebagai berikut: pemilihan pemasok (12 hari) - pelaksanaan teks kontrak (3 hari) - koordinasi dalam layanan fungsional (18 hari) - visa dari orang yang berwenang (3 hari) - memperoleh segel kepala (1 hari) - mendapatkan tanda tangan rekanan (7 hari) - pendaftaran di pihak berwenang (3 hari).
Total kami mendapatkan jumlah waktu yang diperlukan untuk mendapatkan kontrak yang diperlukan - 48 hari. Hasil analisis adalah ditemukannya bottleneck dari skema pengambilan keputusan.
Perubahan utama setelah analisis peta:
- Perintah dikeluarkan untuk mendelegasikan tanda tangan sebagian dokumen kepada kepala departemen (mengurangi beban aparat administrasi dan mengurangi jumlah persetujuan secara signifikan).
- Persyaratan yang sama telah dikembangkan untuk semua layanan (pemahaman umum tentang persyaratan untuk dokumen kontrak, penurunan jumlah kesalahan oleh pelaku).
- Prinsip analisis dokumentasi ujung-ke-ujung telah diterapkan dengan membuat grup spesialis yang sama dari berbagai layanan.
- Menggunakan template kontrak baru.
- Mekanisme pemrosesan dokumentasi melalui sistem elektronik telah dioptimalkan.
- Sistem elektronik untuk melacak kualitas dokumen yang melewati tahapan proses telah dikembangkan.
Hasil utamapemetaan aliran nilai telah menjadi pengurangan 2 kali lipat dalam waktu untuk mendapatkan dokumentasi kontrak, termasuk waktu untuk persetujuan dalam layanan departemen.
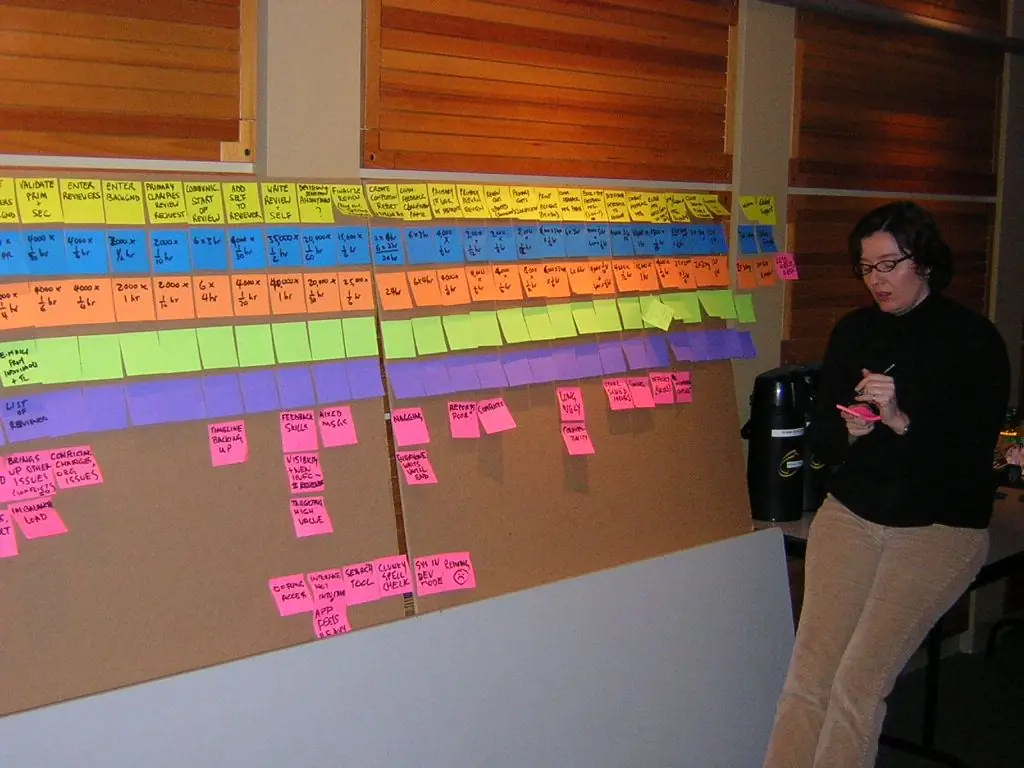
Kesimpulan
Baru-baru ini, pemetaan aliran nilai (VSM, Pemetaan Aliran Nilai) telah menjadi metode yang sangat umum untuk mengoptimalkan pekerjaan berbagai organisasi. Ini karena kesederhanaan dan aksesibilitasnya, biaya minimal dengan efek menguntungkan yang terakumulasi dari waktu ke waktu. Ada banyak contoh keberhasilan penerapan metodologi logistik produksi dasar ini: perusahaan Rostec Corporation, Transmashholding, Kereta Api Rusia, dll. Baru-baru ini, sistem manufaktur ramping telah dibuat di tingkat federal di lembaga medis. Secara khusus diusulkan untuk melakukan pemetaan value stream di poliklinik.
Seperti yang Anda lihat, potensi penuh dari metode yang dipertimbangkan baru saja mulai terungkap.